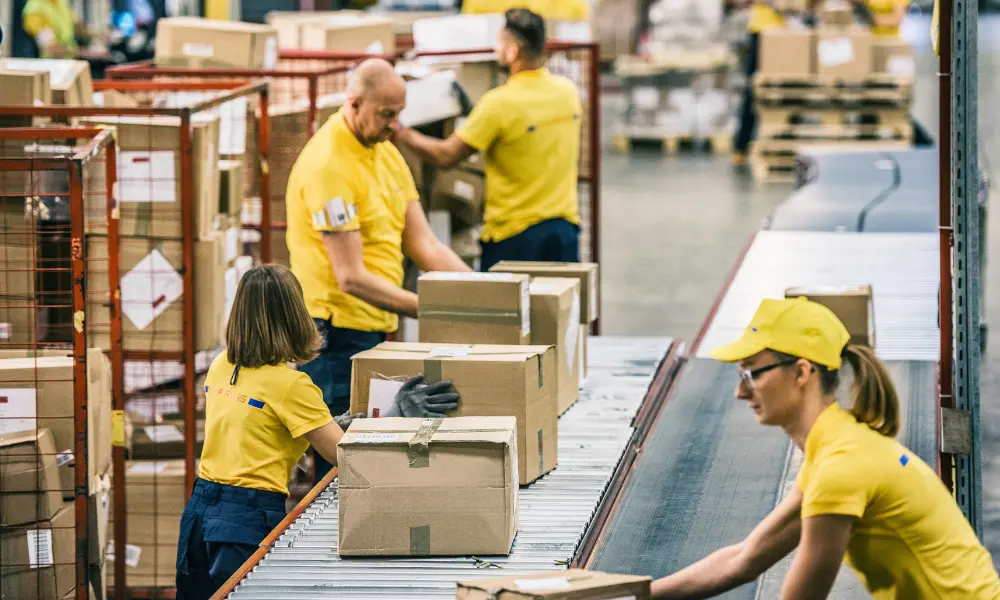
Why does choosing the right supplier impact rotary airlock valve quality?
Manufacturing excellence starts with the precise selection of equipment components that ensure seamless material flow throughout production lines. The integration of high-performance rotary airlock valves plays a vital role in maintaining consistent material discharge rates while preserving system pressure.
Material integrity and system efficiency
Every industrial facility requires dependable components that withstand demanding operational conditions. The selection process considers factors like material characteristics, temperature requirements, and pressure differentials. Manufacturers who prioritize quality in their component selection experience enhanced production efficiency and reduced maintenance needs.
Superior manufacturing standards
Production facilities need equipment that maintains consistent performance across varying operational demands. Engineers focus on dimensional accuracy, surface finishing, and material selection during the manufacturing process. These elements directly influence the longevity and reliability of industrial components.
Quality control measures
Implementing comprehensive testing protocols ensures components meet specified performance parameters. Regular inspections throughout the manufacturing process identify potential issues before they impact the final product. This proactive approach minimizes operational disruptions and maintains system integrity.
Component compatibility
System integration requires careful consideration of how different components interact. R Relationship between equipment specifications and operational requirements ensures optimal performance. This knowledge helps prevent unexpected complications during installation and operation.
Manufacturing expertise requirements
Skilled technicians utilize advanced manufacturing techniques to produce precision-engineered components. Their expertise ensures proper clearances, precise tolerances, and superior surface finishes. These factors directly impact the operational efficiency of material handling systems.
Essential performance factors
The implementation of rotary air lock valve requires careful attention to system requirements and operational parameters. Engineers evaluate factors such as material characteristics, flow rates, and pressure differentials to determine optimal specifications. This comprehensive approach ensures reliable performance across various applications.
Maintenance considerations
Regular maintenance programs extend equipment life and maintain operational efficiency. Technicians monitor wear patterns, bearing conditions, and seal integrity to prevent unexpected failures. This systematic approach reduces downtime and maintains consistent performance levels.
Key performance indicators
- Material throughput optimization
- Pressure differential management
- Energy consumption efficiency
- Maintenance interval planning
- Component life expectancy
- System integration effectiveness
- Operational reliability metrics
- Performance monitoring protocols
System integration requirements
Understanding how components interact within the broader system ensures optimal performance. Engineers evaluate factors such as mounting configurations, drive requirements, and control integration. These considerations influence the overall system efficiency and reliability.
Operational parameters
- Temperature requirements
- Pressure specifications
- Material characteristics
- Flow rate demands
- Clearance tolerances
- Rotation speeds
- Power requirements
- Control interfaces
Installation guidelines
Proper installation procedures ensure components perform as intended. Technicians follow detailed protocols for alignment, connection, and calibration. These steps establish the foundation for reliable long-term operation.
Performance monitoring
It is important to monitor production continuously. Regular performance evaluations enable proactive maintenance planning and system optimization. This approach maintains consistent operational efficiency and extends equipment life.
Industry requirements continue evolving with technological advancement. Understanding emerging trends helps facilities prepare for future operational demands. This forward-thinking approach ensures long-term system viability and performance optimization.
Selecting quality components impacts overall system performance and reliability. The relationship between manufacturing excellence and operational efficiency guides effective decision-making. Industrial facilities benefit from this comprehensive approach because it ensures optimal performance and long-term value.